Cassava is cultivated in 40 African countries, stretching through a wide belt from Madagascar in the Southeast to Senegal and Cape Verde in the Northwest of the continent. Around 70 percent of Africa’s cassava is harvested in Nigeria, the Congo and Tanzania. During the early 1960s, the total annual area of cassava planted in Africa was 5.6 million ha. Thirty-five years later, it had grown to 10 million ha. The six countries that account for most of the cassava grown are the Congo, Côte d’lvoire, Ghana, Nigeria, Tanzania and Uganda. The cassava area planted increased almost threefold in Ghana and Nigeria between 1961 to 1999 (Nweke). This rise has also resulted in increasing cassava waste which is causing environmental and health problems where large amounts of it are being accumulated (Fig. 1).
Cassava and cassava waste in Nigeria
Cassava needs to be peeled before processing, and large-scale cassava processing in Nigeria generates up to 15 million tons of cassava peel waste annually. To make profit from cassava peels and reduce the environmental challenges, the International Livestock Research Institute (ILRI) and International Institute of Tropical Agriculture (IITA), with support from the CGIAR Research Program on Roots, Tubers, and Bananas (RTB), initiated the Cassava Peel Project. The project invested in developing a manufacturing line to convert wet cassava peels into energy-rich high-quality feed ingredients for fish, poultry, large and small ruminants (Figure 2). One ton of high-quality mashes is obtained from three tons of fresh peels; potentially availing five million tons of animal feed ingredients for the country and creating an interesting business opportunity for valorizing cassava waste into a rich source of energy and nutritional for animals.
Scaling cassava peel processing
In 2017, the Cassava Peel Project successfully applied for Scaling Funds from the RTB. Later on, in March 2018, the Cassava Peel Project adopted Scaling Readiness, a novel approach that supports in-depth assessment of the cassava peels processing innovation and its scalability. Scaling Readiness encourages critical reflection on how “ready” innovations are for scaling, and what appropriate actions could enhance scaling.
“The Cassava Peel Project was ready for scaling and we had received funds for that. However, we did not have a clear strategy on how to scale it effectively. Scaling Readiness assisted us in identifying bottlenecks to scaling, and to develop a scaling strategy to overcome bottlenecks”, explains Dr Iheanacho Okike, the Cassava Peel Project Scaling Champion.
Dr Okike added that Scaling Readiness has helped to identify the “soft side” of the cassava peels innovation such as the importance of partnership, user perceptions and pricing mechanisms for scaling it. Prior, the scaling strategy mainly focused on improving the technical components of the innovation, such as the grading machines and the hydraulic press.
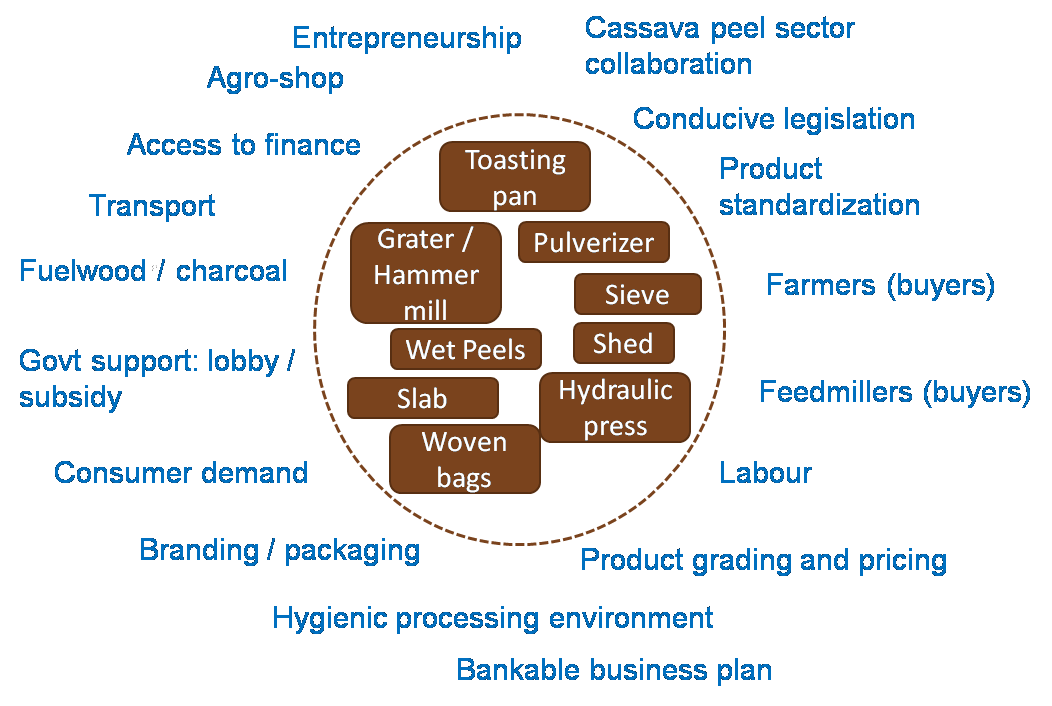
Fig. 3: Soft (blue lettering) and hard (brown lettering, inner circle) components of the High Quality Cassava Peels (HQCP) innovation
Scaling Readiness emphasized that among the biggest bottlenecks were the underdeveloped market for animal feed from cassava waste, as well as overcoming “myths” about cyanide poison in cassava products. Because of the myth, feed millers were not willing to include cassava peels products in their rations. However, the Cassava Peel Project processing steps ensure product safety and hygiene e.g. cyanide and aflatoxin normally present in traditionally processed cassava peel products are reduced to safe limits, leading to High Quality Cassava Peels (HQCP) mashes.
New partnerships for scaling Cassava Peel Processing
To curb the above challenge, the project entered into a partnership and signed a Memorandum of Understanding with Single Spark, to develop an App called FeedCalculator® for making least-cost balanced ratios that includes HQCP mashes as locally available energy ingredient for animal feed. This brought a lot of confidence to millers who see Single Spark as an independent player.
Within the first two years, a total of 2007 ratio formulations included HQCP as fine, coarse or whole mashes. 469 HQCP formulations were made for broilers
Likewise, the project worked with IITA to develop a “Cassava Peel Tracker” platform on the back of its “Cassava Seed Tracker” platform. In developing the Cassava Peel Tracker, 1250 locations were surveyed in four states of South West Nigeria enabling entrepreneurs to locate cassava processing centers nearest to them, with information on quantities of peels available for sale on a daily basis. This also was designed to aid such entrepreneurs to locate their factories central to sources of their raw materials; the cassava peels.
During 2018/2019, 120 potential investors were trained and linked to these sources/apps. A short video on the processing steps has reached 238,000 views on YouTube with 1,100 likes and a large number of email enquiries.
Dr Okike’s five take-home messages from using of Scaling Readiness
The Cassava Peel Processing Scaling Champion, Dr Okike, listed four take-home messages on his experiences with Scaling Readiness:
- Unpacking the innovation and analyzing its different technical and non-technical components using Scaling Readiness revealed constraints to scaling existed within the ‘soft’, non-technical components, including environment and product hygiene, processor/user interfacing, grading and pricing, electricity and labor.
- The structured process can help a process in analyzing the innovation and its readiness for scaling and develop strategies for overcoming bottlenecks for scaling. It also allowed me to decide where we needed to focus on.
- Scaling Readiness supports identifying the ‘right’ partners for innovation and scaling. It supports critical reflection on which partners can help to overcome scaling bottlenecks during the different phases of innovation development, testing and scaling.
- As part of the RTB Scaling Fund initiative, I received support from an experienced Scaling Consultant and a Scaling Readiness Expert. This helped me to set up and implement my project in an impactful manner.
More information:
For more information regarding the CGIAR Research Program on Roots Tubers and Banana (RTB) please visit: https://www.rtb.cgiar.org/.
For more information regarding Scaling Readiness, please visit: www.scalingreadiness.org or contact Dr Marc Schut (m.schut@cgiar.org).
For more information regarding the Cassava Peels Project, please contact Dr Iheanacho Okike (i.okike@cgiar.org).
No Comments